Identifying and Solving Wear and Corrosion Issues
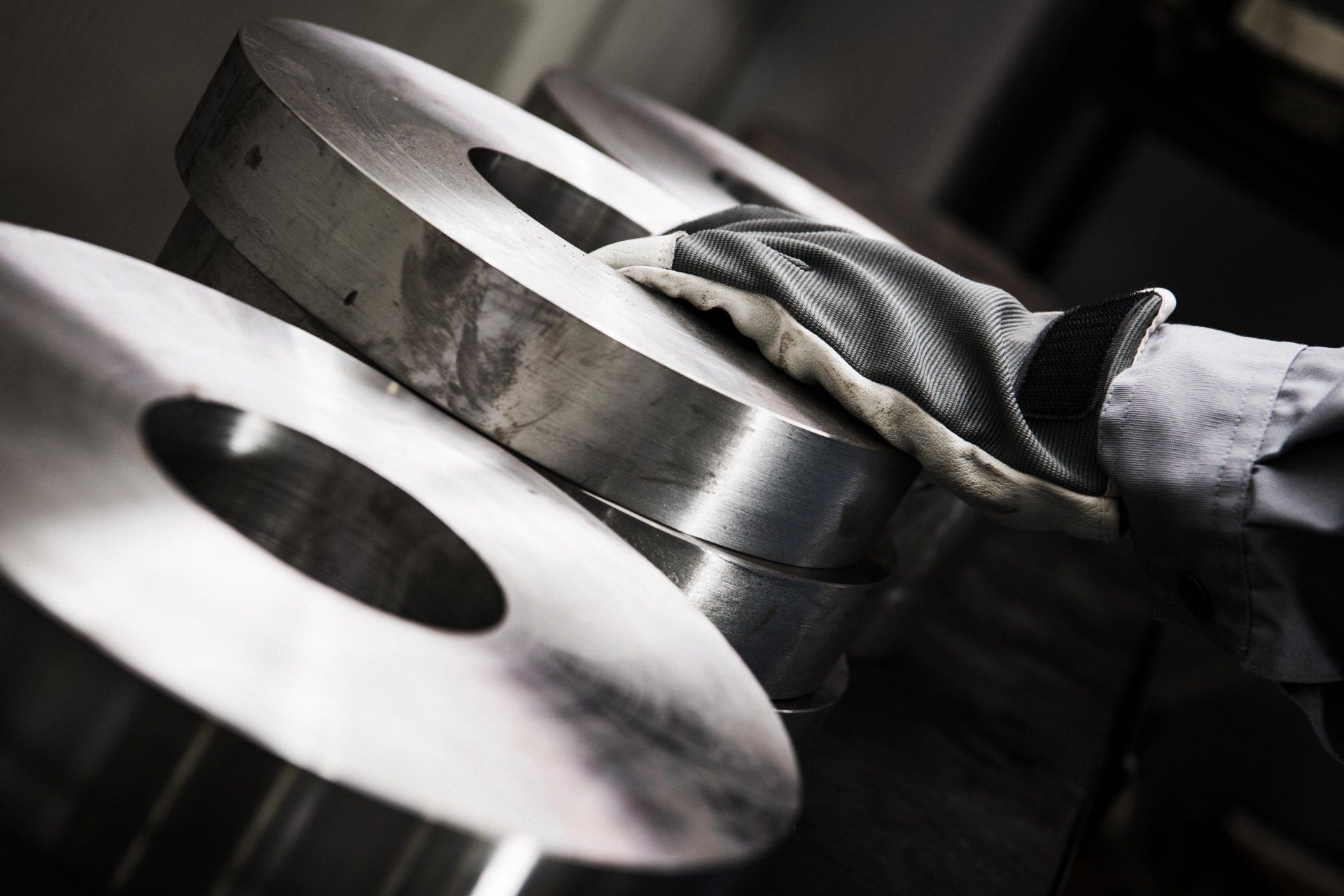
Abrasive Wear:
Abrasive wear is the result of a hard particle or protuberance displacing material as it moves along and against a surface. Abrasion includes cutting or gouging of a surface and often results in loss of material rather than transfer or distortion of material. Grinding, grit blasting, tooling, and polishing are all common examples of abrasion, and patterns of abrasive wear exhibit similar features. Journals, rolls, rotary knives, and pumps are all frequently subjected to abrasive wear. Hayden typically suggests replacing the lost material with a harder material that is less likely to be displaced or ground out by the abrasive. Tungsten carbide, chromium carbide, chromium oxide, aluminum oxide, and some others have the inherent hardness to withstand the abuse of most abrasive environments.
Adhesive Wear:
Adhesive wear is characterized by the transfer or mutual loss of material between two parts sliding or rubbing together under significant force. Specifically, adhesive wear does not involve abrasion, only sliding friction. Some common examples of items prone to adhesive wear include bearings, arbors, shafts, and sleeves. Combating adhesive wear requires reducing the force of friction between the mating components. Hayden typically recommends rebuilding the worn area with a malleable, mechanically “slippery” material, such as aluminum bronze, molybdenum, or alumina titania.
Atmospheric and Salt Water Corrosion:
Corrosion results from the chemical conversion of metals to metal oxides, which often happens naturally over time. An accelerator of corrosive oxidization is an electrolytic liquid, such as salt water or acid rain. Both can quickly deteriorate exposed corrodible materials. The need for protection from these elements lead to the development of a unique coating application, sacrificial corrosion protection. In this process, a readily oxidized material, typically aluminum or zinc, is applied to the surface to be protected. The coating will indeed deteriorate over time, but in doing so it will capture oxygen atoms before they can reach the substrate material. Essentially, the coating “sacrifices” itself to protect the underlying material. Furthermore, a few thousandth of an inch of the coating can continue to effectively protect a surface for several years of continuous exposure to corrosive elements. As an added benefit, the “capturing” behavior of these coatings is capable of reducing or preventing corrosion of adjacent non-coated surfaces. This is especially useful in situations where the line-of-sight thermal spray process is not able to coat every possible crevice or hidden surface.
Clearance Control:
Another application of self-sacrificing coatings is for the establishment of extremely tight tolerances in moving machine parts. More commonly used in aircraft and land-based gas turbine engines and similar environments requiring tight mechanical tolerances, an abradable coating can be applied to one of two surfaces which, by their design, must move with a minimum of clearance between them. The other mating surface is then coated with a wear-resistant carbide coating. This coating can enhance reliable rotary shaft seals eliminating material loss and reducing power consumption. As these parts operate, the friction between the coated surfaces will cause the abradable material to wear. The coating will only wear enough, however, to accommodate the movement of these components. The result is a precision fit between the two surfaces, generous enough to allow free movement but small enough to prevent most materials from passing through. Hayden recommends aluminum graphite, aluminum polyester, and nickel graphite for this application.
Corrosion Resistance:
The corrosive nature of papermaking and similar processes often leads to premature deterioration of machine components from pumps and valves to digesters, rolls, and housings. Hayden offers a range of materials for thermal spray and weld applications that are highly resistant to typical corrosive effects. Materials such as chrome oxide, Hastalloy® and the stainless steels perform well on their own while other materials can be encapsulated and sealed with flame sprayed materials.
Electrical Conductivity:
Thermal sprayed metallics can provide electrical conductivity over most continuous surfaces. A frequent use of this property is to provide uniform EMI and RFI shielding throughout the interior of electronic equipment enclosures. Thermal sprayed copper can be applied to almost any common enclosure material, including plastics and resins.
Electrical Resistivity:
Electrically resistive materials like aluminum oxide can be applied to form a continuous resistive layer over a given surface. A resistive layer sandwiched between a conducting substrate and a conductive metallic coating can be used to create a large-surface resistor with fairly uniform current distribution. This arrangement has been successfully used to create heated drums and rollers designed to replace quartz-lamp-heated rollers used in copiers and printers. The solid, stable nature of a ceramic resistive layer has the added benefit of being free from the problem of lamp burnout.
High-Temperature Fretting:
Abrasion and erosion in extremely high temperature environments poses a unique challenge, as most abrasive wear solutions cannot readily withstand extreme temperature variations, and most thermal barrier coatings are less than ideal in abrasive or fretting wear applications. With the widespread demand for fretting protection inside combustion regions of turbine engines, where components must be both tightly secured and easily replaced, exotic cobalt-based alloys with chrome carbide, tungsten, and other metals have found extensive use. These materials provide exceptional hardness, while readily adapting to the thermal and dimensional changes within this extreme environment.
High-Temperature Oxidization:
Metals exposed to high heat in air or another oxygen-rich environment will typically begin to corrode, even when completely dry. Heat sponsors the combination of oxygen atoms with metallic ions to form oxides, or non-metallic scale. Higher heat typically results in greater acceleration of the corrosive process. One common example of high-temperature oxidization is the accelerated rust scale that forms on steel exhaust piping and mufflers in automobiles. Although it is difficult to prevent this reaction, the process can be slowed by applying a protective barrier or sacrificial coating over exposed surfaces. These coatings slow the combination of oxygen atoms with the metal beneath, and can effectively put a halt on corrosion. Aluminum and some of its alloys, and nickel chromium are excellent high-temperature corrosion control coatings for steel.
Restoration of Dimension:
Perhaps one of the most common repair uses of thermal sprayed coatings and hardface weld overlays is to rebuild material lost through one of the deteriorative processes listed here. Parts may be rebuilt with materials matched to their original construction, or the coating can be used to simultaneously address both dimensional and wear-performance needs. Roll resurfacing, including hard chrome replacement, is one common application that can be used to significantly extend the life of a costly machine component. In fact, the coating will often outperform the component’s original surface because it was tailored to the specific environment in which it was to be used.
Thermal Barriers:
Thermal barrier coatings provide an insulative and heat-dispersing layer between temperature-sensitive components and their high-temperature working environments. This application typically requires more than one layer of coating: A metallic layer distributes heat energy from a point source across a greater surface area, and a ceramic layer, with a high specific heat capacity, provides thermal insulation for the component by slowing the transfer of heat energy to its surface. Thermal barriers excel in environments such as engines and turbines where their purpose is to protect exposed surfaces from the extreme temperatures of combustion. Zirconia alloys such as magnesia and yttria-zirconia perform very well in these environments.
Traction Coatings:
Left unfinished, thermal sprayed coatings typically exhibit a somewhat rough surface profile. Roughness is determined by several factors, including the depth of the grit-blasted anchor profile, the method of application used, and type and size of the material sprayed. Although it is common to grind or polish a component after coating, as-sprayed surfaces, particularly those with some distribution of larger, sharper particles, can be an effective alternative to machine knurling for creating a high-profile traction surface. Learn more about traction coatings >
About Hayden Corp.
Hayden Corp. is the Northeast's only full-service supplier of
thermal spray coating, hardface welding, and machining. Your application is tough - and your market is even tougher. Our solutions-based expert team of craftsmen and technicians know the best solutions that affect your parts.
Contact us for more information and to receive a free estimate.
Questions?
Our staff is always available to answer your questions.
Categories