Plasma Spray Coating
Plasma spray coatings are a versatile and effective way to protect surfaces from wear, corrosion, and high temperatures. Plasma spray can also be used to improve the appearance of surfaces and to repair damaged surfaces. The process of plasma spraying involves heating a material to its melting point using an electric arc or radio frequency plasma plume. The high temperatures of the plasma jet melt the material, which is then deposited onto the coated surface. Plasma spray coatings are often used in high-temperature applications, such as turbine engine components because they can withstand extremely high temperatures. In addition, plasma spray coatings can be used to repair worn or damaged surfaces. Plasma spraying is the most versatile way to apply thermal spray coatings at Hayden Corporation.
Hayden’s plasma spray coating services are available for a wide range of industries, including aerospace, oil and gas, military and defense industrial equipment and components and more. At Hayden Corp, we have the experience and capabilities to handle projects of any size, from a single prototype to large-scale production runs.
Common Plasma Spray Coating Applications Include:
Our state-of-the-art plasma spray equipment is capable of applying coatings with a wide range of properties, including:
- wear resistance
- corrosion resistance
- high-temperature resistance
- electrical insulation
- thermal conductivity
- tribological properties
Additional applications include:
Plasma Spray Coating Process
Low Coating Profile
Like other thermal spray processes, the purpose of a plasma system is to heat and project particles of the material to be applied toward the work surface with as little waste and overspray as possible. Predating the HVOF system, the development of the plasma gun focused only partially on imparting velocity to the powder.
The plasma arc that gives the gun its name was developed as an electrical replacement for the flame used in older flame spray systems. In these guns, the primary objective is to heat the particulate enough before impact that the softened material can easily deform enough to mechanically bond to the surface profile. By connecting opposing poles of a high-potential power supply to a central electrode and concentric nozzle, a high temperature (50,000°F) arc can be created between the two. With the addition of a high-flow-rate inert gas such as argon or nitrogen along the axis of the arc electrodes, the plasma stream can be pushed forward out the front of the gun.
Powder is injected into this hot plasma flame near the front of the nozzle. The arc gas and powder carrier gas expand rapidly in the heat of the plasma flame, and the subsequent velocity propels the hot powder particulate forward.
Plasma Spray Practice
Plasma systems can require some patience during initial setup of parameters, but, once established, the gun can typically run for hours without stopping. This makes it an ideal tool for extremely large parts as material can be applied nearly continuously, stopping only for nozzle inspection or other routine checks.
Without the velocity found in HVOF applications or detonation systems, plasma coatings will typically exhibit less density, and, occasionally, more oxidization. Conversely, they will show lower oxide content and porosity than arc wire or flame combustion deposits.
Plasma Spray Frequently Asked Questions
Submit Your Plasma Spray Coating Project
Hayden Corp is your trusted plasma spray coating expert. Request a quote online or contact our office to learn more about our thermal spray coating services. Hayden Corp is an industry leader in thermal spray coating and laser cladding services for over 100 years. Contact us today!
Sprayed Coatings ▿
Plasma Spray Coating Resources
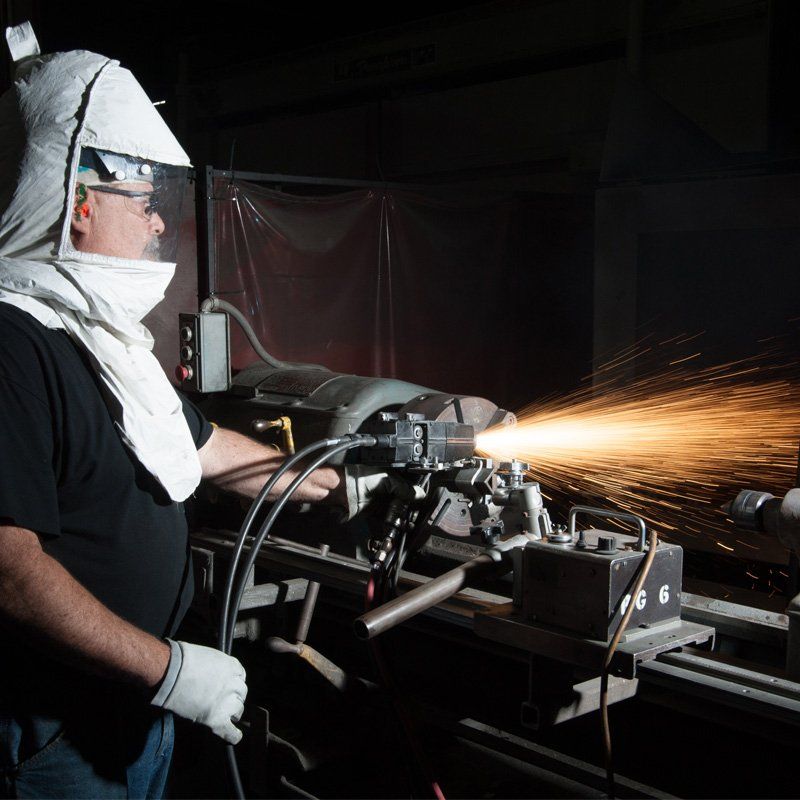
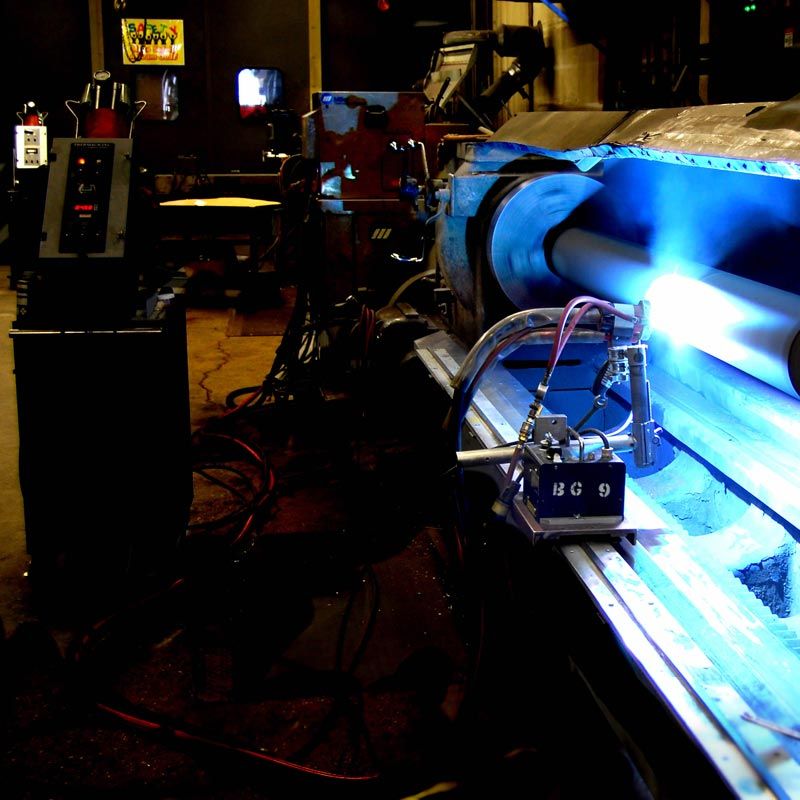
Online Quote Request
Complete our online quote request form below.
We will contact you within the same business day.
Plasma Spray Quote Request
Contact Hayden Corp.
Have a question or have a specific need? Contact our main office or send us a message online.