Laser Cladding Facts
Hayden Corp
Laser cladding offers an array of unique advantages over the conventional welding and hardfacing methods.
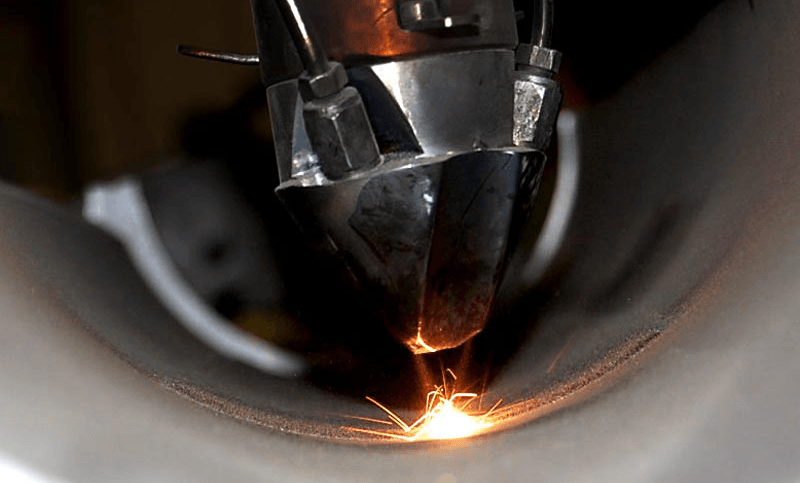
Laser Cladding Facts
- High purity, low dilution welded overlay
Overlay chemistry and hardness are undiluted at the surface of the first pass; there is no need for multiple passes or heavy overlay thicknesses that add expense and induce unwanted tensile stress. - Very low heat input, low distortion
Fully machined parts with close tolerances can be welded with little risk of distortion or dimensional deviation. Overlays have been applied to substrates as thin as 0.060” (1.5mm) without warping or distortion. - Welded, fully alloyed bond
Unlike thermal spray, the bonding mechanism is molecular and not mechanical. External physical stresses are unlikely to cause the overlay to disbond, fracture, or spall. Overlays can withstand significant abrasion and direct impact. - Rugged, high toughness protection
Tungsten and titanium carbide composite overlays are regularly used to protect drilling and mining components. Cobalt-based alloy overlays defend against particulate erosion and cavitation in high-pressure pumps, valves, and turbines. - Impermeable corrosion barrier
Uniform, crack- and pore-free overlays prevent permeation and attack of substrate materials by even highly reactive liquids and gases. Overlays can be machined, ground, and lapped to form tight-fitting seals for valves and couplings. - Virtually unlimited metallic overlay-substrate combinations
Most overlay materials can be welded onto nearly any machinable metallic substrate, allowing high-performance alloys or special property materials to be added strategically to less-expensive free machining steels or exotic aerospace alloys.
For additional information, contact Hayden Corp. by phone (413) 734-4981 or by contacting us online. Visit our laser cladding page to learn more.
Questions?
Our staff is always available to answer your questions.
Categories